芯片电阻器的采用事例(1)
~藉由小型、高耐电压、高精度芯片电阻器来减少零部件数量,提高可靠性~
2022-03-18
汽车电动化的动态始于欧洲发达国家为应对气候变动问题,目前已扩展到了全球范围。数十年后,一些国家将采取只能销售EV(电动汽车)的政策,向EV的转变正在紧锣密鼓迅速推进。
不用说,EV使用电池的功率来转动马达并将其用作推进力,但电池的功率不仅用来驱动主马达,还用来驱动转向、电动车窗的驱动马达、门镜、控制系统、通信系统等车内的几乎所有设备。虽然电池本身的性能有所提高,但与以往将内燃机作为动力的汽车相比,EV的续航里程仍然较短,为了充分利用有限的充电容量,将来自电池的直流电转换为驱动马达所需的交流电的逆变器、和用来尽可能抑制电池劣化以便长期保持性能的BMS(电池管理系统)的作用可以说是非常重要的。
在该逆变器和BMS的电路中大量使用的电阻器,要求具备的特性根据用途会有所差异,而松下电器生产的电阻器具有高电压、高温、高精度等优异的特点,它受到客户的好评且已被客户采用。本次我们将介绍其中的与BMS相关的两个采用事例。
实现电池模块的小型化,降低贴装成本
~在BMS的电压监视/高电压监视电路中使用的高电压用芯片电阻器~
EV的电池进一步连接多个由小型电池单体组合而成的模块来实现高电压。在用于监视该电池BMS电压的高电压监视电路中,在某客户的最高使用电压为1500V的电池的以往设计中,曾将10个2012尺寸(2×1.2mm)的电阻值300kΩ、耐电压150V的薄膜电阻器串联起来使用。对此,被采用的替代方案是将3个松下电器生产的3216尺寸(3.2×1.6mm)的电阻值1MΩ、耐电压500V的薄膜电阻器(产品编号:ERA8PEB1004V)串联起来使用。结果,由10个2012尺寸的电阻器构成时的基板上的贴装面积为40.25mm2,而替换为松下电器生产的薄膜电阻器后,贴装面积则为21.15mm2,此举为减少大约47.5%的面积做出了贡献。
该“ERA8P”系列的容差为±0.1%,温度特性(TCR)为±25(x10-6/K),具有极高的精度。另一个特点是设计时考虑到了可以长期保持这种精度的终生寿命(总容许限度)。具体来说,通过松下电器的独有技术,即可吸收应力的部件材料和巧妙的设计来抑制由于基板和电阻器之间的热收缩差异而导致的焊锡裂纹,这是长期使用时的主要问题之一。一般情况下,电阻器的尺寸越大,由于热收缩差异而产生的应力就越大,但如果采用松下电器生产的芯片电阻器,无论是薄膜类型还是厚膜类型,其连接可靠性都比其他公司的产品优异。
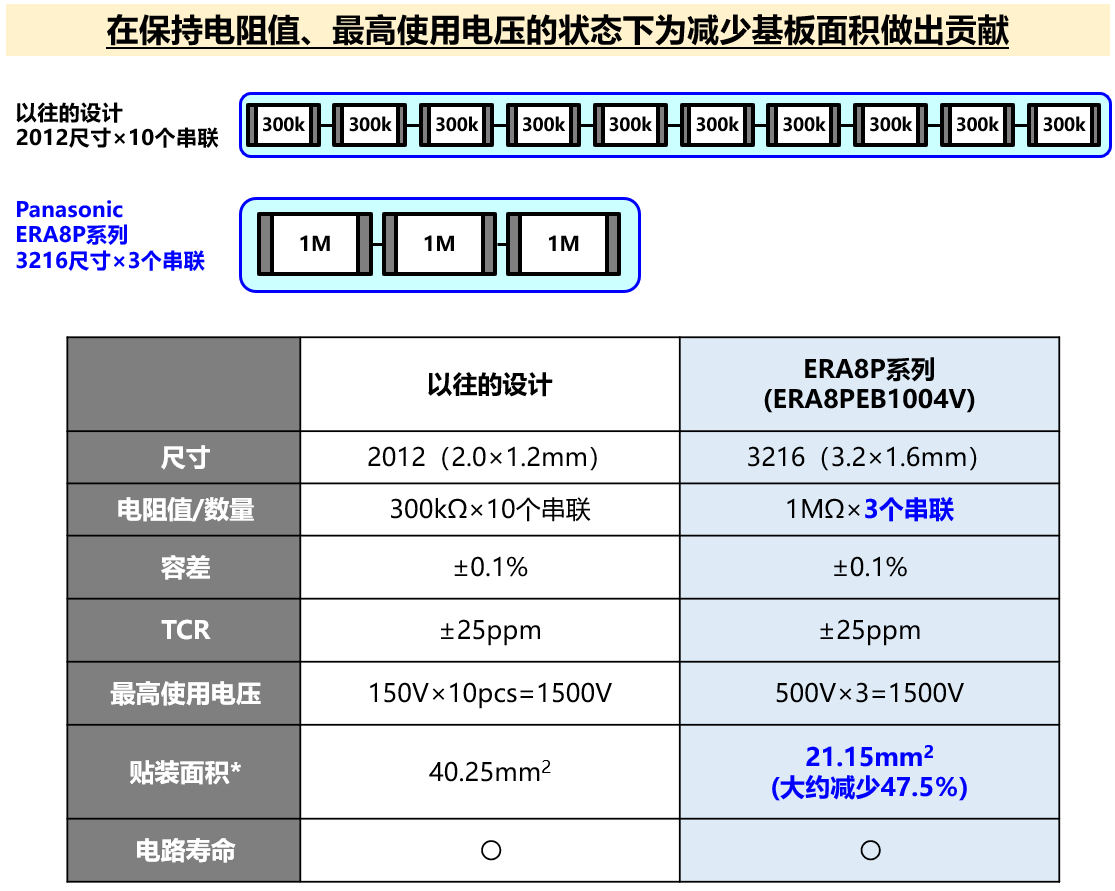
这种终生寿命设计的优点是,电阻值的劣化非常小,并且可以长期、高精度检测电池的劣化状态。由此,可以为EV电池异常时的预兆检测做出贡献。
为大量使用的运算放大器放大电路的小型化、长寿命化做出贡献
在用来将电池电压提高至所需电压的运算放大器放大电路中,使用高精度电阻器。在运算放大器放大电路中,放大倍数基本上是由两个电阻器(R1、R2)的电阻值之比(差值)来决定的,因此并不太需要电阻器的耐高电压性能,但要求其具备非常高的精度。因此,EV制造商越来越多地使用精度更高的薄膜电阻器。
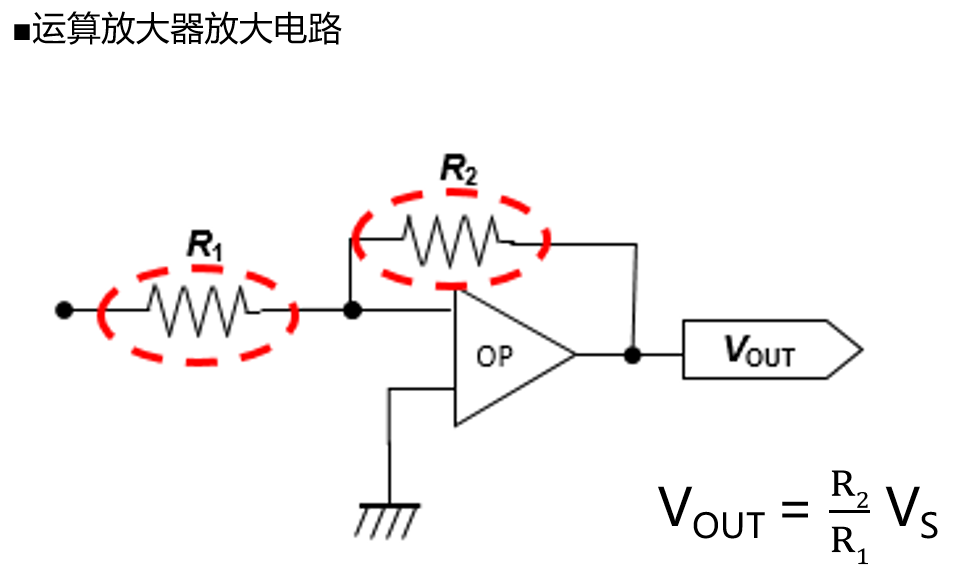
在用于该运算放大器放大电路的薄膜电阻器上,松下电器生产的“ERA*V”系列可以用小一个尺码的产品来提供与其他公司产品同等的性能,因而可以减少基板面积。以1608尺寸(1.6×0.8mm)、额定功率0.1W、最高使用电压75V为例,通过用松下电器生产的薄膜电阻器1005尺寸(1.0×0.5mm)、功率0.1W、最高使用电压75V的“ERA2V”系列来替换,贴装面积可以大约减少60.3%。
与厚膜电阻器相比,薄膜电阻器通常存在着对过载和静电放电(ESD)的冲击电压较弱且易损坏的缺点。但是,松下电器生产的“ERA*V/K/P”系列采取了ESD预防措施,其设计考虑到了人体所带的静电(1k~1.5k伏)。具体而言,2012尺寸保证可达2kV,1608尺寸保证可达1.5kV,1005尺寸保证可达1.0kV,这是业界最高等级(截止到2022年3月)。
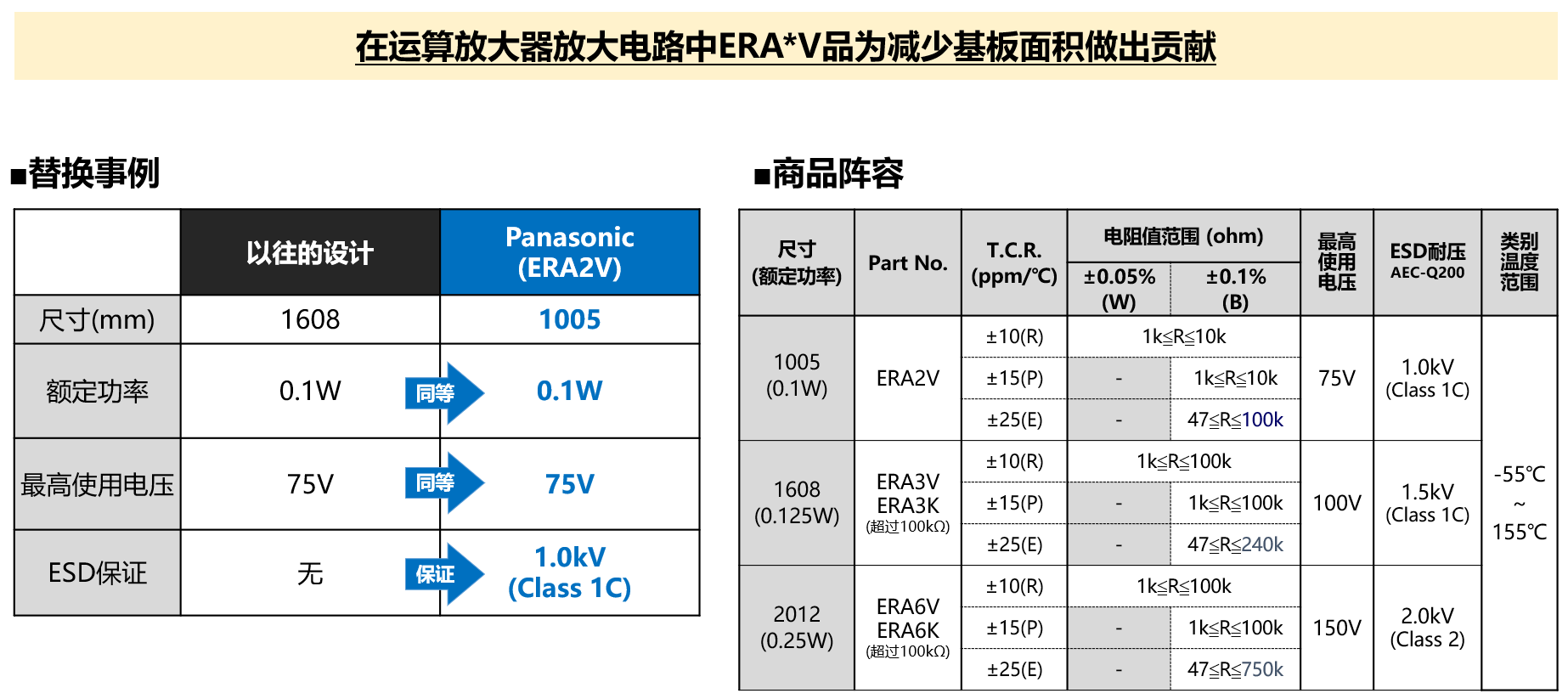
同样,对于被视为薄膜电阻器弱点的热冲击(贴装后的热收缩)引起的焊锡裂纹、锡焊时使用的助焊剂进入引起的电解腐蚀(硫化特性),我们还提供具有抗冲击或抗腐蚀特性的高可靠性和高耐候性产品。与以往产品和其他公司产品相比,这些优异的特点是通过材料和设计的重审来实现的。
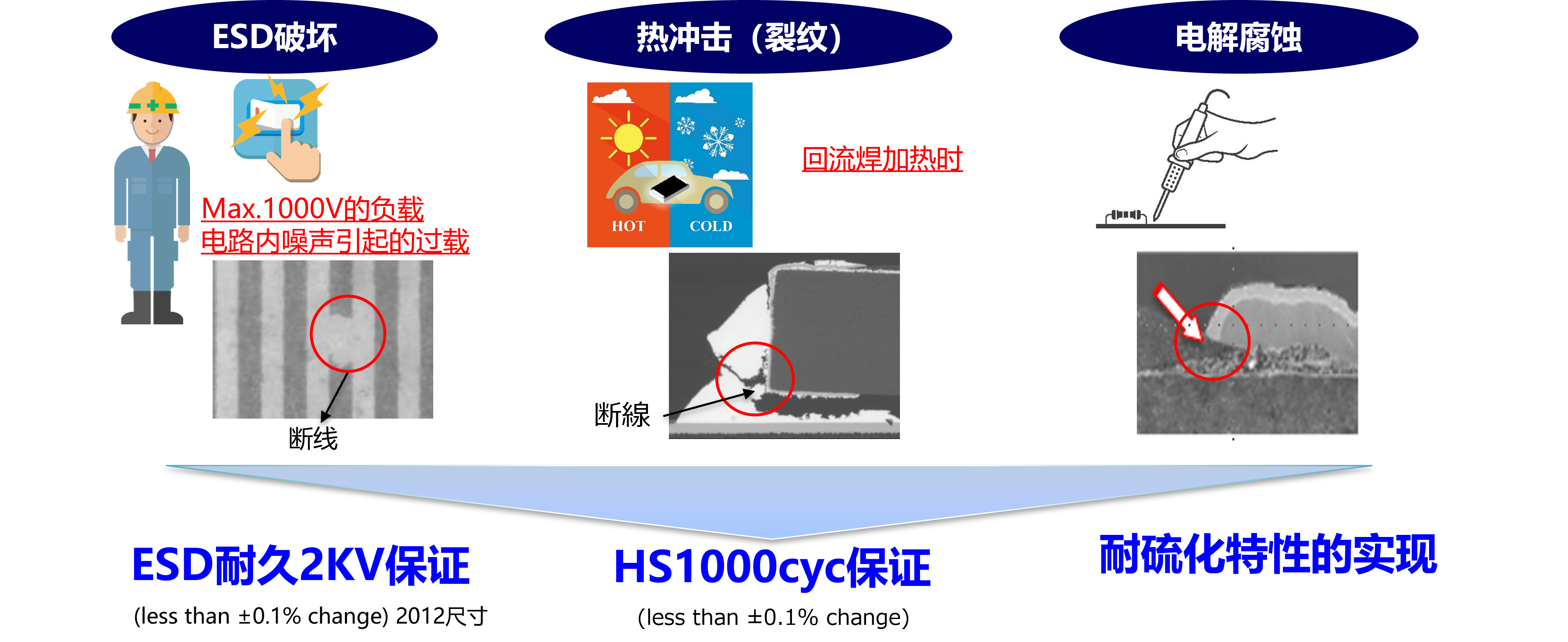
通过藉由松下电器的独有技术实现的兼备小型、高可靠性、高耐候性的薄膜电阻器,为减少贴装面积,降低成本,提高可靠性做出贡献。